The Best Argument for using the Construction Hub: It Saves Money
- news and press
- Apr 18
- 4 min read
The Best Argument for the Construction Hub: It Saves Money
For many years, there has been extensive discussion about improving construction logistics, especially considering their environmental impact. The call for sustainability in the construction sector is growing louder, and rightly so—more and more reports are being expected that provide transparency about the CO₂ emissions resulting from construction activities. Still, the construction industry is not easily convinced to take voluntary steps toward more sustainable logistics. Often, real change only comes under pressure from regulations, such as mandatory use of construction hubs.
In a recent article on logistiek.nl (April 2025), Hans Quack rightly observes that the use of urban logistics hubs is often seen as an added expense: “...the cost savings a hub is supposed to deliver do not always outweigh the extra costs of using it.” A critical observation, and one that holds true for many traditional hubs. However, Quack also acknowledges that specialized hubs—like construction hubs—can, in fact, be economically viable and highly effective. And that’s exactly the core of the argument.
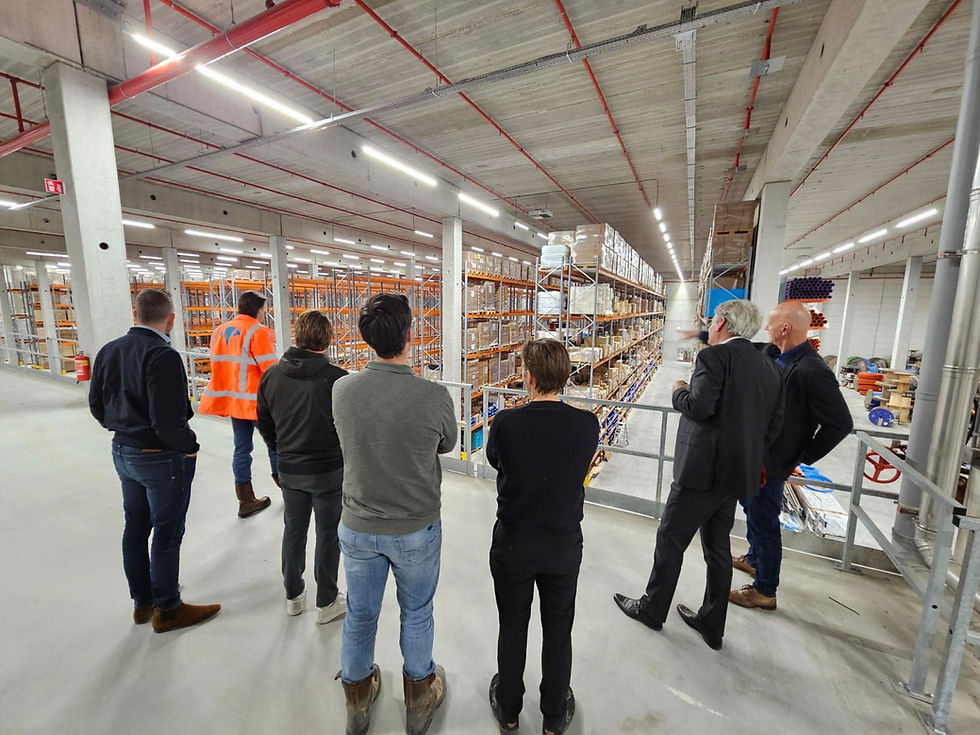
Why a Construction Hub Works—And Saves Money
A common misconception about logistics hubs in the construction sector is that they are merely additional links in the chain—storage areas where goods sit idle, with their only advantage being that they facilitate emission-free urban delivery. But a construction hub is much more than that. Unlike generic logistics hubs that simply act as transfer points and focus on electric city transport, a construction hub is fully integrated into the construction process itself.
A well-organised construction hub already generates cost savings before the goods even arrive. It starts with collaboration with suppliers. By agreeing on delivery times, consolidating shipments, and optimizing load efficiency, transportation to the hub becomes more streamlined. Fewer trips, fuller loads, better planning—all of this directly reduces fuel costs, improves logistics planning, and minimizes staffing needs.
Once the goods reach the hub, they are not merely stored—they are strategically prepared for just-in-time delivery to the construction site. This ensures that materials arrive exactly when they’re needed, without cluttering the site or requiring additional storage space. As a result, the footprint of the site can be smaller, and construction time can be reduced—and in construction, time quite literally equals money.
Smart Construction Logistics: Bundled prefab; "buildings Packages" and Specialisation
Another major benefit of the construction hub is the ability to create bundled construction kits. Instead of delivering miscellaneous pallets with various materials, complete kits can be assembled that are tailored to each phase of the construction process. This saves time on-site, reduces errors, and enables a smoother workflow. Less searching, less damage, less material waste. Altogether, this leads to substantial cost savings.
It is important to emphasize that a construction hub is run by specialized professionals who understand the construction sector. They know the dynamics, the time pressure, and the unique requirements of construction projects. These hubs also have vehicles tailored to construction logistics: trucks with cranes, compact city-friendly vehicles, and electric delivery options for zero-emission transport. This combination of expertise, equipment, and process management transforms a construction hub from a cost center into a cost saver.
Construction Hubs: Collaboration Instead of Obligation
It’s essential to realize that a construction hub is not a burdensome mandate that increases building costs. On the contrary, it is a strategic partner that collaborates with construction companies to streamline the entire logistics chain. By consolidating deliveries, optimizing transport, aligning material delivery with project phases, and ensuring professional handling, construction logistics become not only more sustainable but also significantly more cost-effective.
Where traditional logistics providers often simply move goods from point A to point B, a construction hub adds real value by improving processes, reducing waste, and shortening project timelines. It’s about more than just transport—it’s about managing the entire logistics workflow.
Numbers That Speak for Themselves
Let’s look at some concrete figures: on average, logistics accounts for approximately 15% of total construction costs. At the same time, the average profit margin for construction companies in 2024 was just 2.4%. This means that even a modest improvement in logistics efficiency can have a massive impact on project profitability.
Using a construction hub can result in significant savings within the logistics portion—sometimes up to 30–40%. When these savings are scaled to the overall project cost, they can make the difference between a project operating at a loss or at a profit.
Conclusion: The Construction Hub as an Essential Link
The time when construction hubs were viewed as a mere added expense is behind us. Today’s construction hub is a smart, integrated solution that contributes not only to more sustainable construction logistics but also to considerable cost savings. Through collaboration, specialization, and process optimization, the construction hub helps make the industry future-proof—and more profitable.
In short, the strongest argument for implementing a construction hub is simply that it costs less. It’s not a burden, but a pathway to better outcomes. Smart construction companies don’t adopt construction hubs out of obligation—they embrace them out of conviction.
Would you like a shorter summary for use in a brochure or presentation?
Comments